Built for winter exploration, MSR snowshoes offer high quality, technical performance for everyone from casual winter hikers to serious mountaineers. One of the ways MSR developers maintain their high level of quality and innovation is by manufacturing their snowshoes in Seattle. Making their snowshoes in-house allows for greater communication between designers and production techs and gives MSR better control of each step in the process. Let’s see how MSR’s pinnacle Lightning Ascent snowshoes are built.
Manufactured in Seattle
All MSR snowshoes have been made on-site in Seattle since the 1995 launch of the Denali Classic snowshoe. Working from a concept by renowned inventor and big wall climber Bill Forrest and developed using MSR technology and engineering, the Denali featured traction bars and crampons made of strong martensitic steel in a design that revolutionized the snowshoe industry.
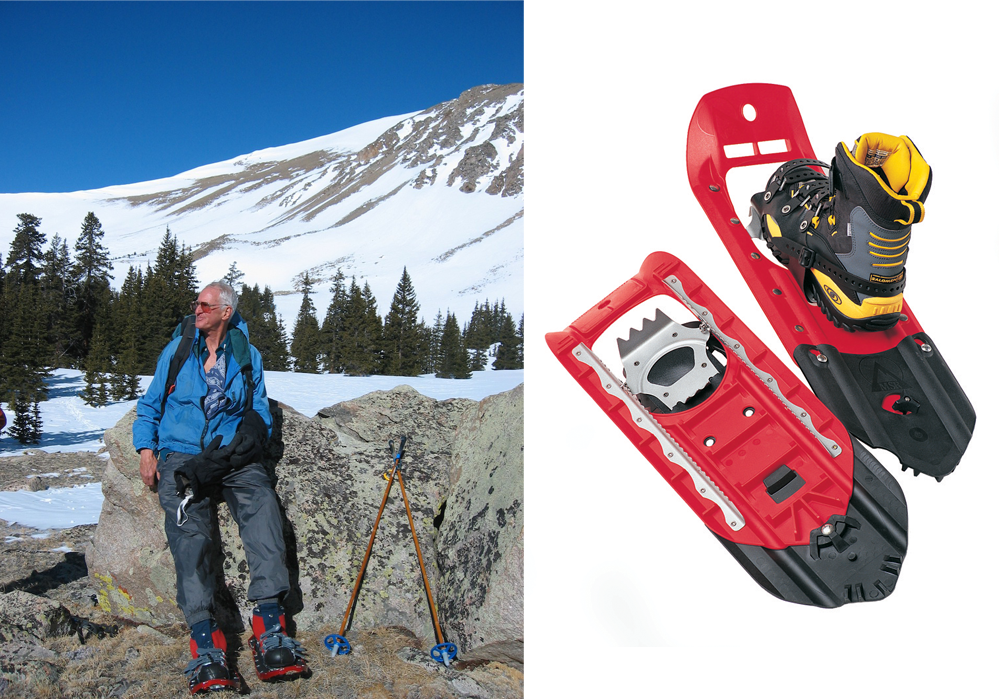
Bill Forrest from the MSR photo archives (left) and MSR Denali Classic Snowshoes, 1995 (right)
Such a breakthrough design deserved the close supervision that MSR’s on-site manufacturing offered. Today, this tight oversight ensures MSR snowshoes meet the company’s goal of creating functional and reliable gear. And it provides them with an opportunity to learn from the manufacturing process itself.
The Process: Making the Lightning Ascent Snowshoe
For a look behind the scenes, let’s follow the MSR Lightning Ascent snowshoe through its fabrication and assembly process.
The first piece created is the snowshoe’s aggressive 360-degree traction frame. A large laser cutter produces multiple snowshoe frames at once from a single blade of strong, ultralight 7000 series aluminum.
Each laser-cut frame is then shaped into 360 degrees by a programmable bending machine, creating the snowshoe frame. This bending operation is crucial to the design’s functionality, and the on-site quality checks help ensure that each Lightning Ascent snowshoe works as it’s supposed to.
A massive 400-ton punch press sits on its own isolated 5-foot thick reinforced concrete foundation in the factory.
Guided by a single operator, the 400-ton punch press fabricates other snowshoe parts, such as the frame’s cross members and crampons, which are then attached at key points in the assembly process, speeding efficiency and reducing labor costs.
After the 360-degree traction frame is bent and riveted in one station, the frame is sent out to a local paint house to receive a powder coating. When it returns, the riveting machine operator attaches a special polyurethane fabric decking—which is also die-cut in-house. This high-tensile fabric is what gives the Lightning Ascent snowshoe its ultralight flotation. Oversight is critical during this part of the process because the fabric must be cut and riveted to the deck in precise angles to tension the frame for proper flex and function.
Offsite, the bindings, also made of polyurethane (a cold-resistant, flexible plastic used on all our snowshoe bindings), are injection-molded. The parts are delivered to the Seattle factory where they are assembled and riveted to the crampons. Then the whole binding-and-crampon assembly is attached to the snowshoe deck frame and voilà: a brand new Lightning Ascent snowshoe.
Design and Manufacturing Efficiency
MSR matches its efficient snowshoe designs with an efficiency of manufacturing because attending to both product and process ensures that only quality gear goes out the door. MSR’s machines are created in its own on-site tool shop and are regularly maintained by the toolmakers to assure they are operating on spec. Making snowshoes in Seattle has also allowed MSR employees to learn how to deal with disposable waste material and recycling, so they can maintain their goals of environmental and socially conscious manufacturing. They strive to be good stewards and that begins at home.
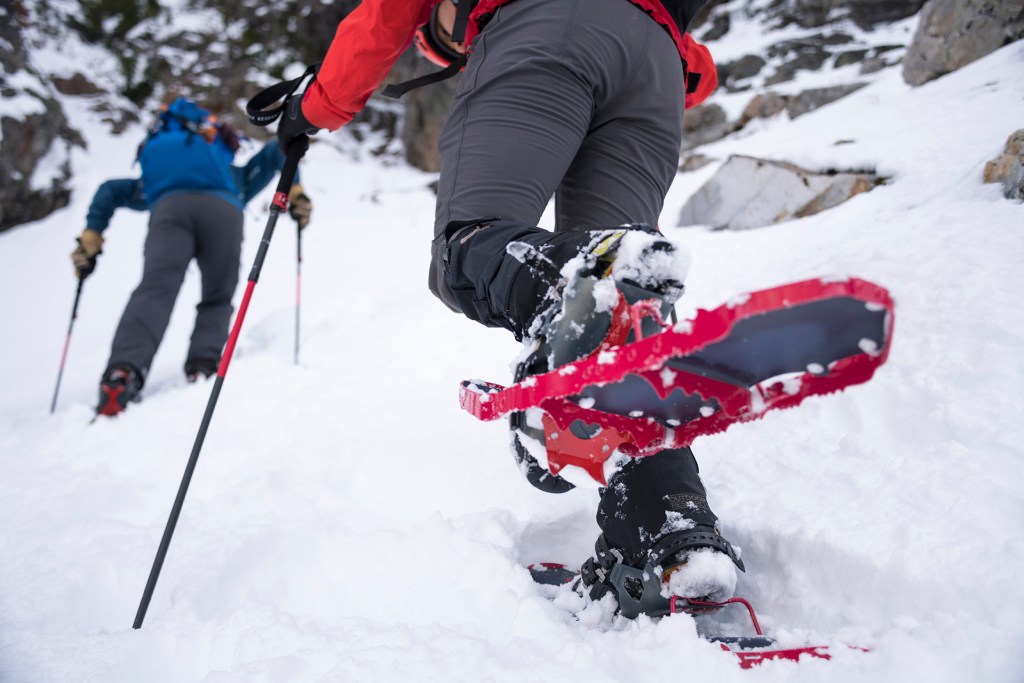
Photo Credit: Scott Rinckenberger
Learn more about MSR and their products on The Summit Register.