We have a plastic problem: we’re practically swimming in the stuff. Most Americans realize that our issue with plastic waste is an environmental crisis affecting virtually every marine and freshwater ecosystem out there. And yet, we keep churning out single-use plastic at an incomprehensible speed. According to the data, we could have more plastic by weight than fish in the ocean by 2050. In the United States alone, nearly 60 million single-use plastic water bottles are tossed in the trash each day. Even scarier: that number reflects a mere fraction of the daily plastic waste thrown out worldwide with one report detailing global consumption of 1 million plastic bottles every single minute.
So yes, we have a massive plastic problem. But thanks to a new material by Eastman Specialty Plastics, brands like Nalgene, CamelBak and HydraPak may have the beginnings of a solution. The secret: Tritan Renew, a BPA-free material derived from 50% recycled content, or waste plastic. While the concept sounds simple, the science behind the technology is anything but basic.
“This is like the Holy Grail of reusable water bottles,” says Eric Hansen, marketing director for Nalgene Outdoor Products. “We’ve all been searching for this for over a decade.”
The magic behind Tritan Renew exists thanks to a special type of recycling used to convert waste plastic into consumer products like reusable water bottles. Originally, Eastman tried to use mechanical recycling, a more traditional approach that transforms plastic waste by grinding, washing, separating and compounding the polymers into new plastic materials. However, Eastman was unsuccessful in that approach. In 2019, they arrived at Nalgene’s Tennessee production factory to begin working on chemical recycling, the superstar process that makes Tritan Renew possible.
Eastman uses something called polyester renewal technology (PRT), a chemistry process that breaks down waste plastics (like single-use water bottles) into molecular building blocks. No mashing or smashing is needed; the transformation is done at a molecular level. Then, those particles can be reused and constructed into new plastic products, like Tritan Renew.
“It’s just as durable as the old Tritan that we used for years, only now half of it is recycled content,” Hansen says. “We have a reusable container, we took it one step further, and now it’s almost a closed loop.”
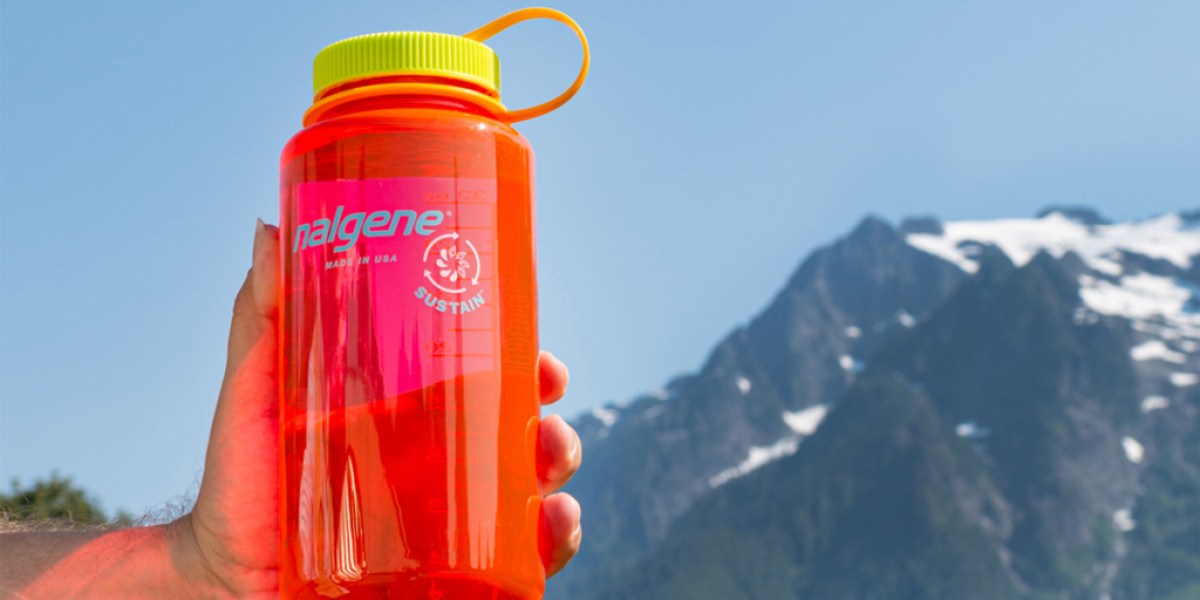
That’s the crux of the conversation: the closed loop. Hansen is referencing the notion of a circular economy, the gold standard in sustainable manufacturing. This differs from the historically popular linear economic model that follows a “take-make-waste” plan where we take materials, make a product, and then throw it away. Instead, a circular model has three main tenets: keep products and materials in use as long as possible, design products with minimal waste and pollution, and emphasize renewable and recycled materials. This way of doing business reduces pressure on the environment while also minimizing human impact on our finite resources.
While the circular model isn’t yet a fully closed loop for Nalgene, Tritan Renew takes them a few steps closer with their new water bottle line. Called Sustain, the line exclusively launched at REI in August 2020 and uses the recycled plastic to produce reusable bottles that are meant to stay in rotation for quite a long time. Moreover, the recycled content in a single Sustain bottle is the equivalent of eight plastic single-use bottles. Nalgene hopes to eventually develop a program where they take old water bottles made from Tritan Renew and manufacture them into new product (the bottles are currently made from #7 plastic and may be recyclable in your region). For now, the new line both eliminates consumers’ needs for single-use bottles and minimizes a fair bit of the waste plastic headed for our oceans. As an added bonus, using recycled waste plastic reduces 50% of the fossil fuel resources originally needed to make a single reusable water bottle.
And Nalgene isn’t the only brand stepping into this space. According to Danielle Deal, senior category merchandise manager for REI, CamelBak and HydraPak are now making water bottles made with Tritan Renew. The language is tricky since each brand is calling their new line something different. Nalgene went with Sustain while CamelBak opted for Renew and HydraPak chose Recon. But while the language varies, the material is the same: bottles constructed with 50% recycled content. This shift is critical for REI as stores will only carry the recycled content bottles moving forward.
“The co-op has a climate commitment, which includes a pledge to reduce its carbon footprint by 55% in the next ten years,” Deal says. “It sounds like a long time but there shouldn’t be any delay in moving assortment decisions in the right direction. That’s the only way to make a deep impact.”
Hansen agrees. In fact, he doesn’t think Nalgene is even close to done yet.
“Our plan is to eventually get to 100% recycled content,” he says. “We’re not there yet from a technology perspective, but that’s definitely the plan.”
For more stories of brands doing good work, visit our Good Gear landing page.