For years, Smartwool designers stared at socks’ innards and saw the potential to revolutionize apparel construction. In a technical sock, cushiony, plush zones transition into meshy, sweat-venting zones without seams for improved comfort. Designers dreamed of bringing that variable construction to base layers—if only there was a machine that could knit complicated pants and shirts.
Now, they have one. After nearly 10 years of tinkering, Smartwool’s designers figured out a way to knit Merino wool base layers that hug the body’s every curve, bump and taper, just like a simple tube sock. Through its Intraknit 3D knitting techniques, Smartwool merges various types of fabric into shapes that mirror the body’s irregularities. The first Intraknit base layers, available in two fabric weights (200 and 250), arrived at REI in August. Not only do they deliver unprecedented comfort, but they require less material and generate less waste than traditional cut-and-sew constructions.
“Intraknit is the biggest innovation in apparel manufacturing in 200 years,” says Anne Wiper, Smartwool’s vice president of product. In the mid-1800s, the invention of the sewing machine revolutionized apparel construction. Now, 3D knitting allows for another leap forward in construction capability.
That may sound like overheated marketing hype, until you consider how long humans have been cutting pattern pieces out of sheets of cloth. Ever since the prehistoric invention of the fabric loom, people have traditionally made clothes by trimming shapes out of big rectangles of material. But that method creates a lot of wasted fabric scraps (an estimated 5 to 10 percent loss, according to Smartwool). What’s more, stitched seams can feel rough on the skin—and achieving a close, articulated fit requires many seams.
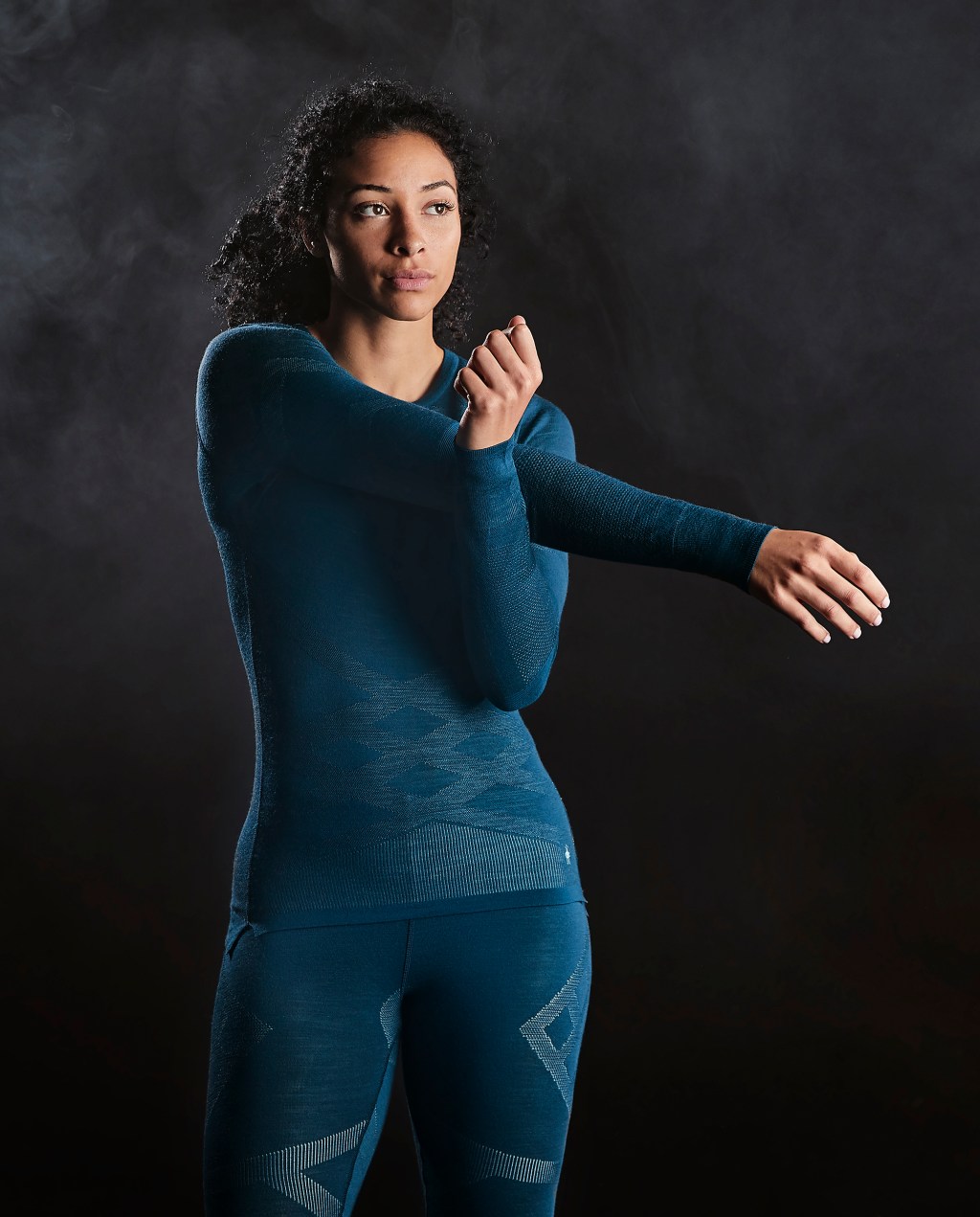
Smartwool’s Intraknit Merino 200 Crew Base Layer Top is 3D-knitted, which means it has top-level fit and no seams.
In modern apparel manufacturing, fabric mills produce large rolls of material that are shipped to other factories to be cut and sewn into garments. But 3D knitting eliminates that entire step: Intraknit garments go from yarn to finished product in one leap, with virtually no waste. Smartwool is still in the process of quantifying 3D knitting’s environmental benefit, but, says Wiper, “it’s big.” Not having to produce, finish and ship bolts of fabric saves energy; knitting garments (rather than cutting and sewing them from sheets) eliminates scraps.
“Our goal [at Smartwool] is to be zero waste,” Wiper says. 3D knitting moves the company closer to that goal.
The manufacturing technique also produces performance apparel that’s markedly more comfortable than Smartwool’s traditionally constructed base layers. In part, that’s because of the articulation: The Intraknit 200 Crew (women’s, men’s), for example, features a bend in the elbows that’s achieved with knitted shaping in lieu of seams. The Intraknit 200 Bottom (women’s, men’s) does the same thing at the knees. The resulting fit is cleaner, with less sagging.
And variations in the fabric’s warmth and ventilation improve the base layers’ ability to regulate the wearer’s body temperature (like a sock). Back in 2011, VF (Smartwool’s parent company) commissioned a 1,200-person study to evaluate the skin-temperature differences between women and men: Body-mapped data revealed precisely where these genders tend to run hot and cold. Smartwool used those insights to design Intraknit pieces that boost insulation where wearers trend cold and vent heat from their warmest zones.
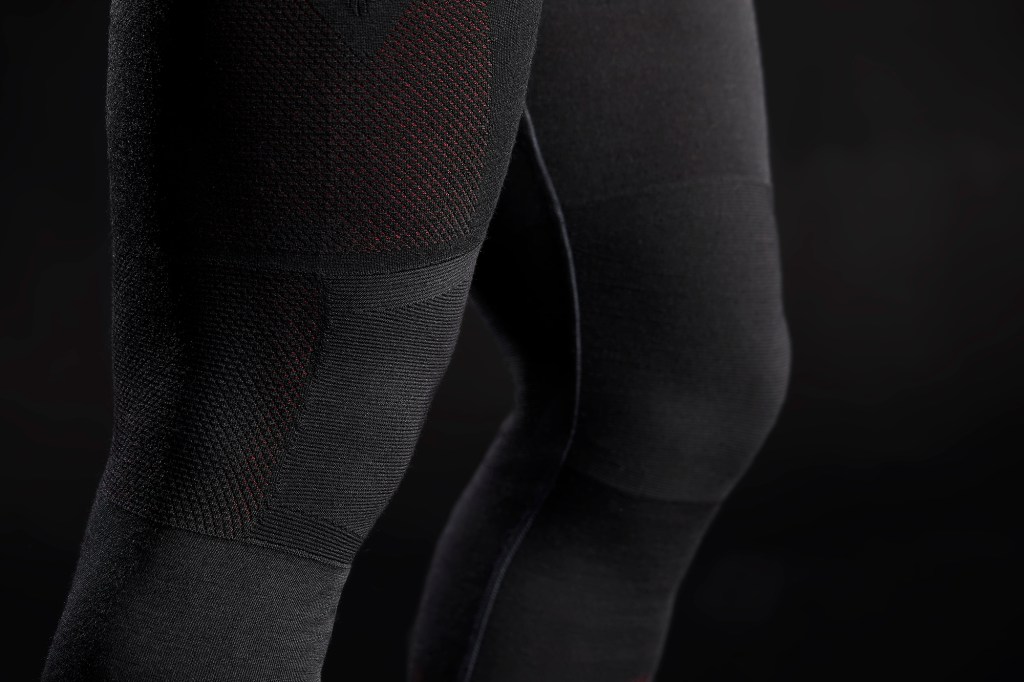
The Intraknit 200 Bottom is articulated at the knees.
The Intraknit Merino 250 Thermal Quarter-Zip—which is the warmer of the two Intraknit weights that Smartwool debuted for fall 2019—places terry-looped insulation (like the interior of bath towels) across the collarbones and shoulders of the men’s version, while the women’s top uses it across the chest. The women’s Intraknit Merino 250 Thermal Bottom adds insulation across the seat and upper thighs (where women trend colder) but the men’s version only uses it across the back waist.
The lighter-weight Intraknit Merino 200 Crew and Bottom also customize the thermoregulation. Although there are no terry-looped insulation zones, there are denser-knit portions (across the chest) and ventilating zones (in the crotch and upper chest).
But Smartwool designers also know that most consumers just want to wear clothes they can forget about. “Really, the goal of a designer is to create apparel that moves with you, so you’re not aware of your clothing,” Wiper says. She feels like 3D knitting does that better than any other method of apparel construction.
“People have been knitting socks and sweaters, but these [3D knitting] machines let you do so much more, with far better fit,” she explains.
Smartwool intends to expand the program far beyond Intraknit’s initial launch. For fall 2019, the Intraknit 200 Crew and Bottom combine Merino wool with virgin (new) polyester to create a faster-drying fabric, but by fall 2020, the brand plans to use recycled synthetics. Forthcoming pieces will also feature more patterns and colors.
Across the apparel industry, Wiper expects the 3D knitting trend to grow. Already, companies like Nike (with its Flyknit innovation) have demonstrated knitting’s potential for footwear.
“Three-D knitting has opened up a whole new way of constructing garments,” Wiper says. No longer are manufacturers obliged to stitch together shapes cut from sheets; suddenly, clothing design seems like a boundless frontier. Says Wiper, “It’s a wide-open opportunity right now for those that know how to get after it.”